Find
Walking toward the parking lot at the end of
the 2003 Rochester NY Hamfest, I found this
VTVM on the ground in a free giveaway pile.
I didn't "need" an antique VTVM, but this
one visually stood out from the usual junk
items: it was only a bit grimy and dusty,
not rusty. It was missing 3 of 12
front panel screws, but it had all the knobs
and controls, as well as the probe and
ground cables. The gleaming chrome
engraved front panel and meter had nary a
scratch. I told the guy monitoring the
pile I would restore it, and it was mine.
Inspection
Once home, I looked inside before trying to
power it up on the variac. The power
cord (apparently original) was intact, but
cracked stiffly as I uncoiled it. The
inside was dusty, and flakes from of the
mouldering cotton insulation on the power
transformer secondary wires fell away with
the slightest touch. All 4 of the
tubes were present, and three of them were
loctals (locking octals). I observed
no signs of burning or other distress
inside, but I concluded that the mains cord
and power transformer leads should be
fixed before applying power. A quick
search of the internet yielded no schematics
or operating manual. While it wasn't
safely usable as-is, the VTVM's engraved
front panel alone justified the space
it would occupy on my mad scientist lab
shelf until I felt competent to tackle its
issues. I put the cover back on,
cleaned the exterior, and put it on the
shelf.
Resurrection
Eight years later I had gained the
experience and patience I thought I would
need to restore the antique VTVM to safe
operation. This time, an internet
search for "Philco 7001" brought me to this
Philco
Phorum article. Chuck Schwank,
who curates The
Philco Repair Bench, has schematics
for almost every piece of antique Philco
gear, and will send you a well-made copy of
the operation manual for $7. Several
days later Chuck provided me with my own
copy and I was ready to begin. The
document included the current Philco test
equipment price list. The 7001 VTVM
was the highest priced item in the list, at
$104.50 1947 dollars!
Priorities
My goal for this restoration was to obtain a
working VTVM. The best restoration
would preserve all the functional original
parts, and use cosmetically accurate
substitutes for anything that needed to be
replaced. While I believe the
effort to do this is justified for rare or
sought-after articles, I didn't feel this
unit qualified for that level of
attention. My personal priorities were
to restore safe operation, to simplify
future maintenance, and to make no
mechanical alterations (e.g. no holes
drilled or structural parts filed) that
would complicate a future "perfect"
restoration by someone with more patience,
more skill, and less sanity than I have.
AC mains power
The instrument left the factory with a
two-wire power cord, non-polarized plug, no
mains fuse, and "death caps" between both
legs of the AC line and ground. I
believe it is best to use a modern 3-wire
power cord, to fuse the hot lead before the
power switch, and to remove the "death caps"
on the AC line. I also prefer to be
able to replace the power cord without
soldering. To this end, I snipped the power
cord and death caps at the terminal strip
where these met the power transformer
primary and power switch leads. I installed
a fuse clip in the space vacated by the
death caps, attached by a simple bracket
made from scrap steel to an existing
structural screw. Inside the case, I
terminated the hot and neutral legs of the
AC line with a two position molex connector,
with its mating with connector on the mains
cord. I installed a rubber grommet in
the existing line cord entry hole, fed the
new 3 wire cord through the grommet, and
secured it to an existing screw for the
carry handle with a nylon cable clamp
. I soldered a ring terminal to the
mains cord safety ground wire and secured it
to one of the other carry handle
screws. I could have used a modern
Heyco-style strain relief, but that would
have required enlarging the existing line
cord entry hole. The rubber grommet
looks more "period", and the internal nylon
clamp provides the required anti-yank
resistance. |
Power transformer leads
I snipped all the power transformer leads at
the terminal strip and rectifier tube
pins. Removing the power transformer
required disassembling nearly everything
attached to the front panel, as the nuts
securing it to the mechanical structure were
inaccessible. This was more than I had
intended to do, but provided me with the
opportunity to do more thorough internal
cleaning down rthe line.
My original plan was to sleeve all the
deteriorated transformer filament and high
voltage secondary lead insulation with
modern flexible fiberglass "spaghetti"
obtained from Radio
Daze. However, even the large
#11 size would not fit over the ragged
breaks in the cotton insulation. I
decided to disassemble the transformer end
bells, to remove the existing insulation
from the secondary wires all the way back to
the transformer core, and to sleeve them
with #20 size fiberglass spaghetti.
This worked out well for the HV leads, but
halfway down one of the filament leads, the
stranded wire itself broke off, leaving it
too short to use. I finished removing
the filament lead insulation, sleeved the
segment between the core and break
with fiberglass, and solder spliced a new
pair of filament leads using modern stranded
transformer lead wire. I sheathed the
spliced area with the #11 fiberglass secured
with heatshrink tubing. The primary
leads and secondary center tap lead were
insulated with PVC that was still in good
condition, so I did not have to intervene
there. The original and repaired leads
emerged from the reassembled transformer end
bells in good condition. A full
cosmetic restoration might have used modern
lacquered cotton-covered wire in the
original colors, but I was content to use
modern materials. The resistances of
all transformer windings were in near
perfect agreement with the values shown on
the schematic.
In addition to replacing the transformer
leads, I also replaced the shielded cable
between the terminal strip connecting the AC
mains leads to the power switch. It
also showed ragged cotton insulation and
flying bits of shield braid. I didn't
have an appropriate piece of shielded
control cable handy for this repair, so I
made my own shielded cable. I encased #20
stranded teflon wire with braided shield,
covered the braid with the #11 fiberglass,
and secured the ends of the fiberglass with
heatshrink tube. It was more labor
than it needed to be, but it looks at least
as nice (though not historically accurate)
as the original. Philco's use of
shielded wire here showed some care in
manufacture. The general quality of
soldering and wiring layout is typical for
TV's or radios of the time, rather than the
higher standards of Hewlett Packard or
Tektronix instruments that appeared later,
but I didn't observe anything really
offensive. |
Several
views of the VTVM before restoration
|
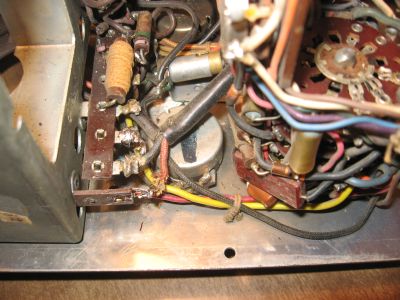 |
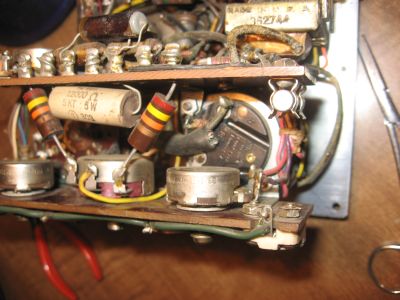 |
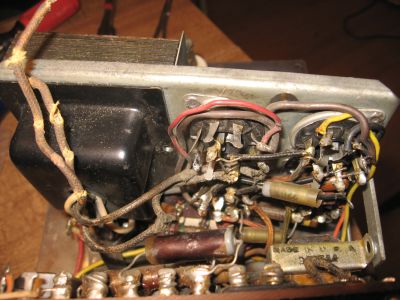 |
|
Filter capacitor
The power supply filter capacitor was a
cardboard-sheathed single section 20 uF 450V twist
lock FP type. While there were no signs of
leaking electrolyte, I decided to replace it with a
modern 22 uF 450 volt radial lead electrolytic
attached to a new terminal strip fastened to an
existing structural screw near the location of the
original capacitor. Alternatively, I could
have performed a more cosmetic restoration by
attempting to reform the original capacitor, or
replacing the contents of the original can with a
modern cap. Since I preserved the original
capacitor, I still have this option. However,
I was more interested in determining whether the
instrument would function well before I invested too
many hours on appearance.
Internal cleaning
As a side effect of having to detach the entire
structure of the instrument from the front panel in
order to remove the power transformer, I obtained
much better access to the two bakelite terminal
boards containing all the internal adjustment pots,
wiring, and components that were not attached to
tube pins and selector switch terminals. I
cleaned the boards with numerous cotton swabs
moistened with drug-store 91% isopropyl alcohol
(IPA), taking care not to soak the cotton-insulated
wire and custom-wound precision resistors on the
boards. I hoped that the benefit of removing
conductive dust from the boards outweighed the risk
of damaging the wiring or components with the IPA.
I treated the front panel zero adjust and range
pots, as well as the two four-deck selector switches
with Caig Deoxit.
I carefully removed all old solder and bits of wire
left on the terminals and tube pins from which I had
previously snipped the wires. This is one of
my least favorite restoration tasks, as it's a pain
to manipulate soldering iron, solder wick, solder
vacuum, picks, and tweezers in the cramped confines
of point-to-point wiring. It's one reason why
I'd rather scratch build new equipment on turret
boards than restore old point-to-point wired gear.
I worried that if the instrument did not work at the
end of this modest restoration project, I might feel
compelled to tear it apart and rebuild it to my
semi-mil-spec standards. I imagined the
excruciating tedium of desoldering and cleaning
every terminal on the selector switches, and the
worry vanished.
Things left alone
Other standard steps when restoring antique
electronics include checking carbon composition
resistors for drift, and replacing all paper
capacitors. Philco used good quality resistors
in this unit, as all of the carbon comps were still
well within tolerance. The manual emphasized
the quality of the new (for that era) ceramic
encased resistors used for all critical circuit
elements. They were all spot-on.
However, several tubular capacitors were
tucked into relatively inaccessible locations, and I
wasn't really sure what would make the best modern
replacements. I hoped that Philco paid as much
attention to the capacitors as they did to the
resistors, so I left them alone until after
functional tests and calibration. Also all the
tubular caps are in low voltage dividing or
compensating positions, so I reasoned that they
might be less prone to DC leakage.
I chose not worry about the tubes (7Y4 recifier, 2 x
7B5 bridge amps, and 6SN7 bridge) before testing the
instrument. None of them are operated anywhere
close to a limit, so apart from mechanical shock or
a disasterous electrical stress, they should last
forever in VTVM service.
The meter movement was made by Simpson, another sign
that Philco chose quality parts for this
unit. The meter rectifier was a stack of
four tiny copper oxide diodes. I hoped it was
still in good shape.
The outside of the case is finished in a hammertone
dark turquoise enamel, with one signifcant chip
missing from the paint, and plenty of smaller
ones. It would be tempting to strip and
refinish it back to factory, but not justifiable for
this level of restoration. Once of the four
felt-covered bottom feet was missing, and replaced
with a washer and a #10 screw by the previous
custodian. There are also 3 missing front
panel screws, #6 x 1/2" slotted round head. Modern
galvanized steel screws look too shiny.
Stainless looks good with the chrome front panel,
but I think that I will just scavenge vintage
replacements from some non-restorable discard.
These things can wait for my next outbreak of
boredom, or a more fanatical restorer. |
Pictures of
the VTVM after restoration
|
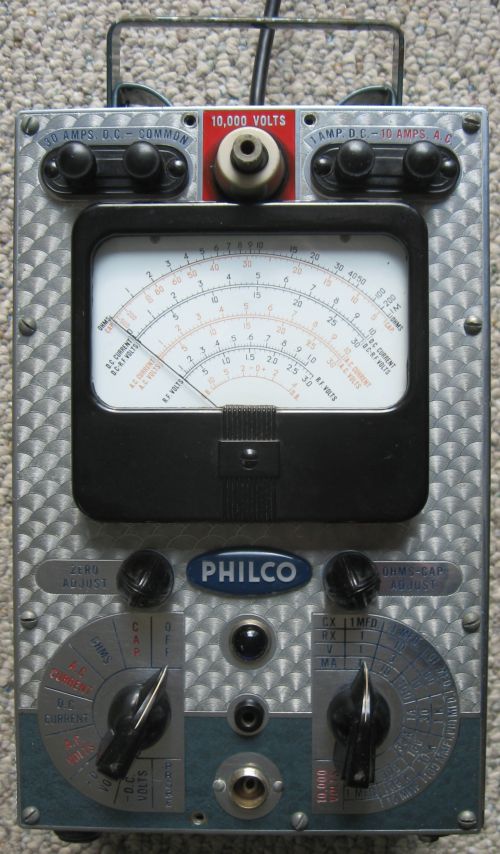
|
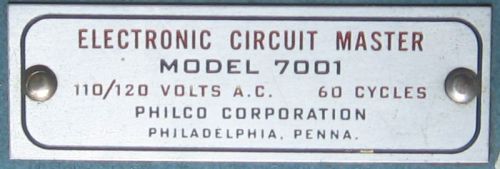
|
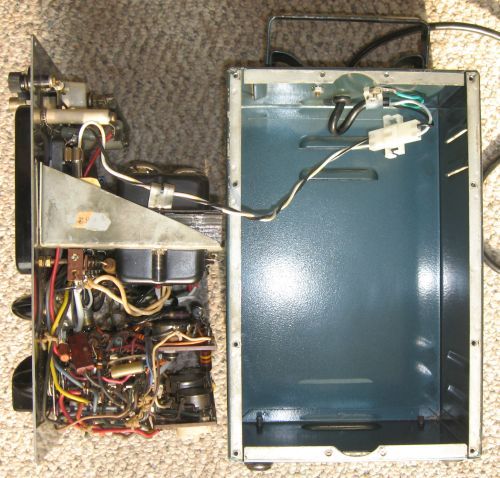
|
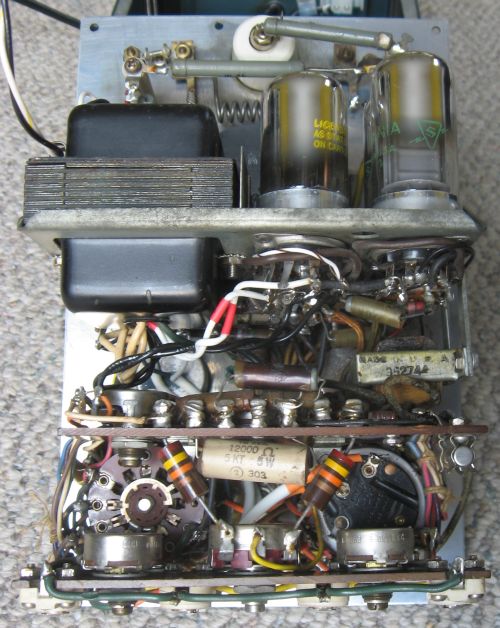
|
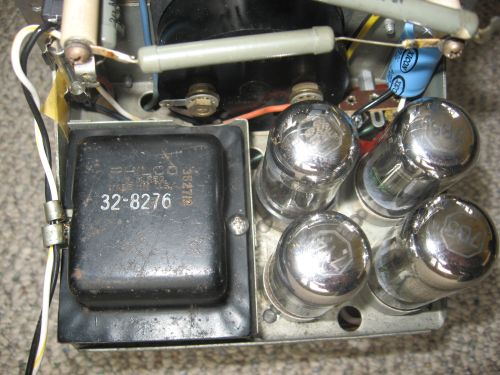
|
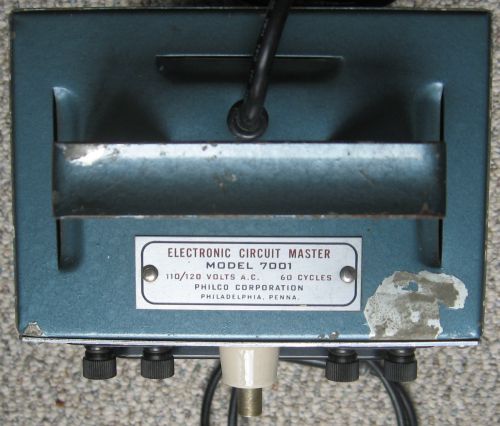
|
|